Erik Hauri
Lumber -> Guitars
BH-8 chambered singlecut multiscale 8-stringer
OK so this is a collaboration with Ben to build a chambered singlecut 8-string bass/guitar hybrid instrument and a multiscale on top of it (why not, right?). The design borrows from some obvious influences, but also benefits from some improvements to the body design, neck joint and layout of the multiple scales. There are some cool features to the build that will be good to document.
Heres the menu:
Walnut chambered body core
Figured claro walnut top, back & headstock lam with wenge accent layers
5-piece maple-walnut neck with CF reinforcement
Tru Oil finish
29.5 to 25.5 scale, 7th fret perp
Bartolini humbuckers and paired P-bass pickups (passive)
Master Vol (push-pull coil tap) & Tone, 3-way switch for humbuckers
Stacked Vol-Tone for bass pickups
Separate outputs for bass & guitar pickups
Ben will be using this for pursuing some new directions in jazz guitar I am almost as anxious as he is to hear what he can do on this thing.
Here are some shots of the claro top with the body outline superimposed the knots in the center will be mostly routed out in the pickup routs by angling the bookmatch seam.
Gotta have a template:
Neck lams are individually milled in the drum sander.
This might be the first photo I’ve shown of my glue press – pretty simple, a set of 2” high aluminum angles to keep everything dead straight and distribute the pressure from 8-10 bar clamps. Trigger clamps at the ends and in the middle (through a hole in the table) keep all the lams firmly down against the table. Wax paper underneath so I don't glue the neck to the bench....
Carbon fiber bars routed and installed. I like the System 3 epoxy adhesive for all my epoxy gluing tasks (resin 105 and slow hardener) – it is very forgiving in the mix ratio, so that you can use pumps instead of measuring with a scale.
OK so this is a collaboration with Ben to build a chambered singlecut 8-string bass/guitar hybrid instrument and a multiscale on top of it (why not, right?). The design borrows from some obvious influences, but also benefits from some improvements to the body design, neck joint and layout of the multiple scales. There are some cool features to the build that will be good to document.
Heres the menu:
Walnut chambered body core
Figured claro walnut top, back & headstock lam with wenge accent layers
5-piece maple-walnut neck with CF reinforcement
Tru Oil finish
29.5 to 25.5 scale, 7th fret perp
Bartolini humbuckers and paired P-bass pickups (passive)
Master Vol (push-pull coil tap) & Tone, 3-way switch for humbuckers
Stacked Vol-Tone for bass pickups
Separate outputs for bass & guitar pickups
Ben will be using this for pursuing some new directions in jazz guitar I am almost as anxious as he is to hear what he can do on this thing.
Here are some shots of the claro top with the body outline superimposed the knots in the center will be mostly routed out in the pickup routs by angling the bookmatch seam.
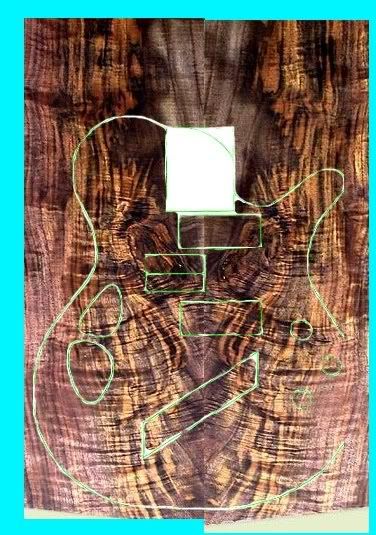
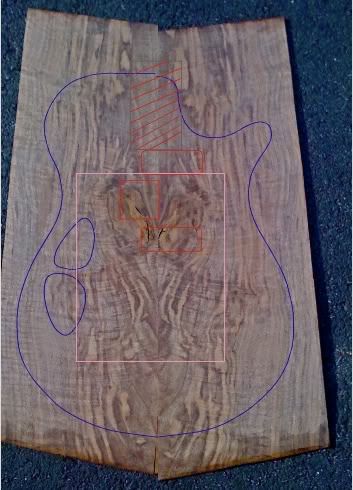
Gotta have a template:
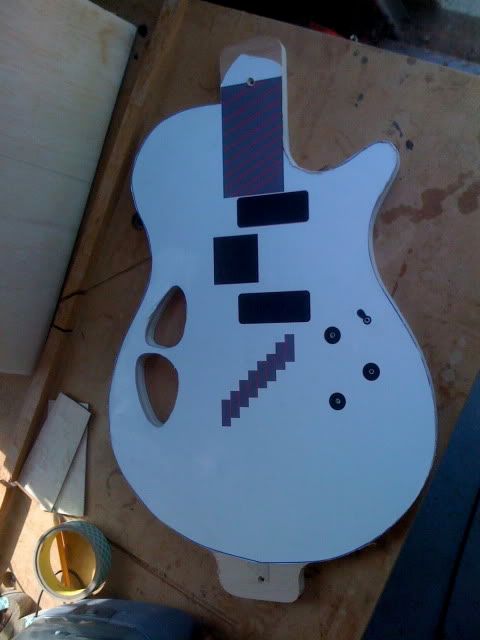
Neck lams are individually milled in the drum sander.
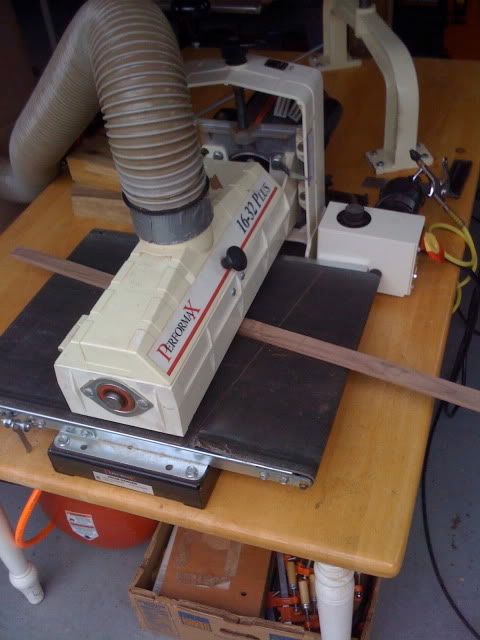
This might be the first photo I’ve shown of my glue press – pretty simple, a set of 2” high aluminum angles to keep everything dead straight and distribute the pressure from 8-10 bar clamps. Trigger clamps at the ends and in the middle (through a hole in the table) keep all the lams firmly down against the table. Wax paper underneath so I don't glue the neck to the bench....
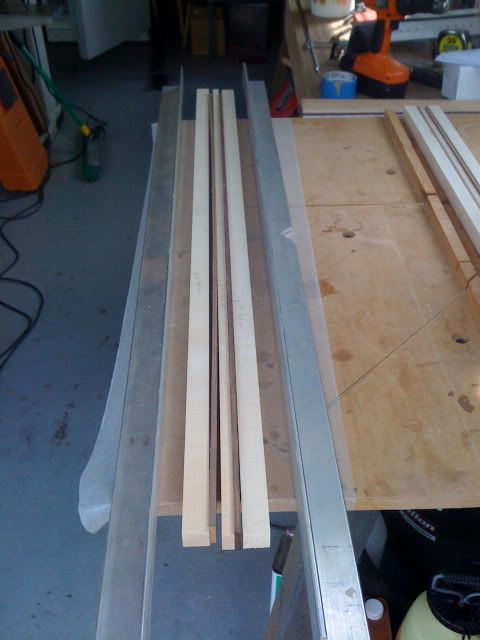
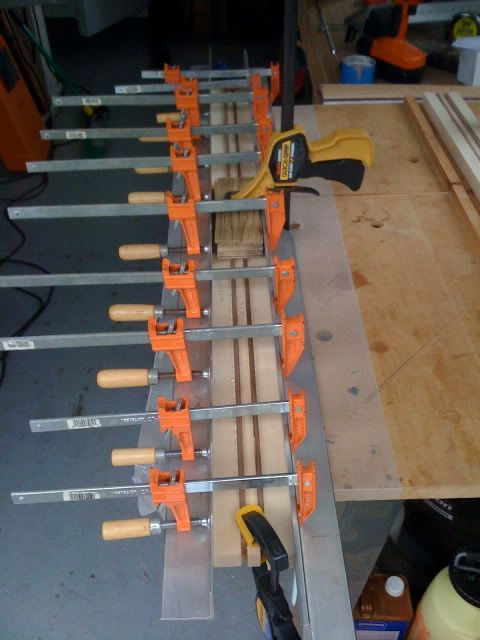
Carbon fiber bars routed and installed. I like the System 3 epoxy adhesive for all my epoxy gluing tasks (resin 105 and slow hardener) – it is very forgiving in the mix ratio, so that you can use pumps instead of measuring with a scale.
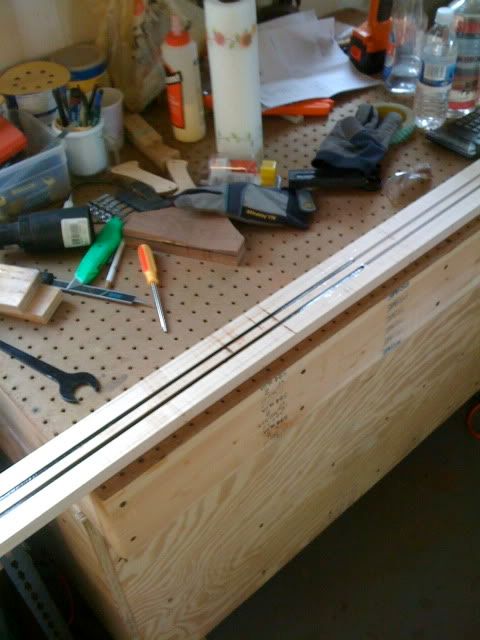